The Discovery and Uses of Metals
What would human civilization look like without metal? The discovery and understanding of different metals and alloys have shaped the way humans lived, fought, and made progress. From the early years of the bronze age to the more recent uses of stainless steel, few things have had as much influence on the world as metal.
Historical Timeline
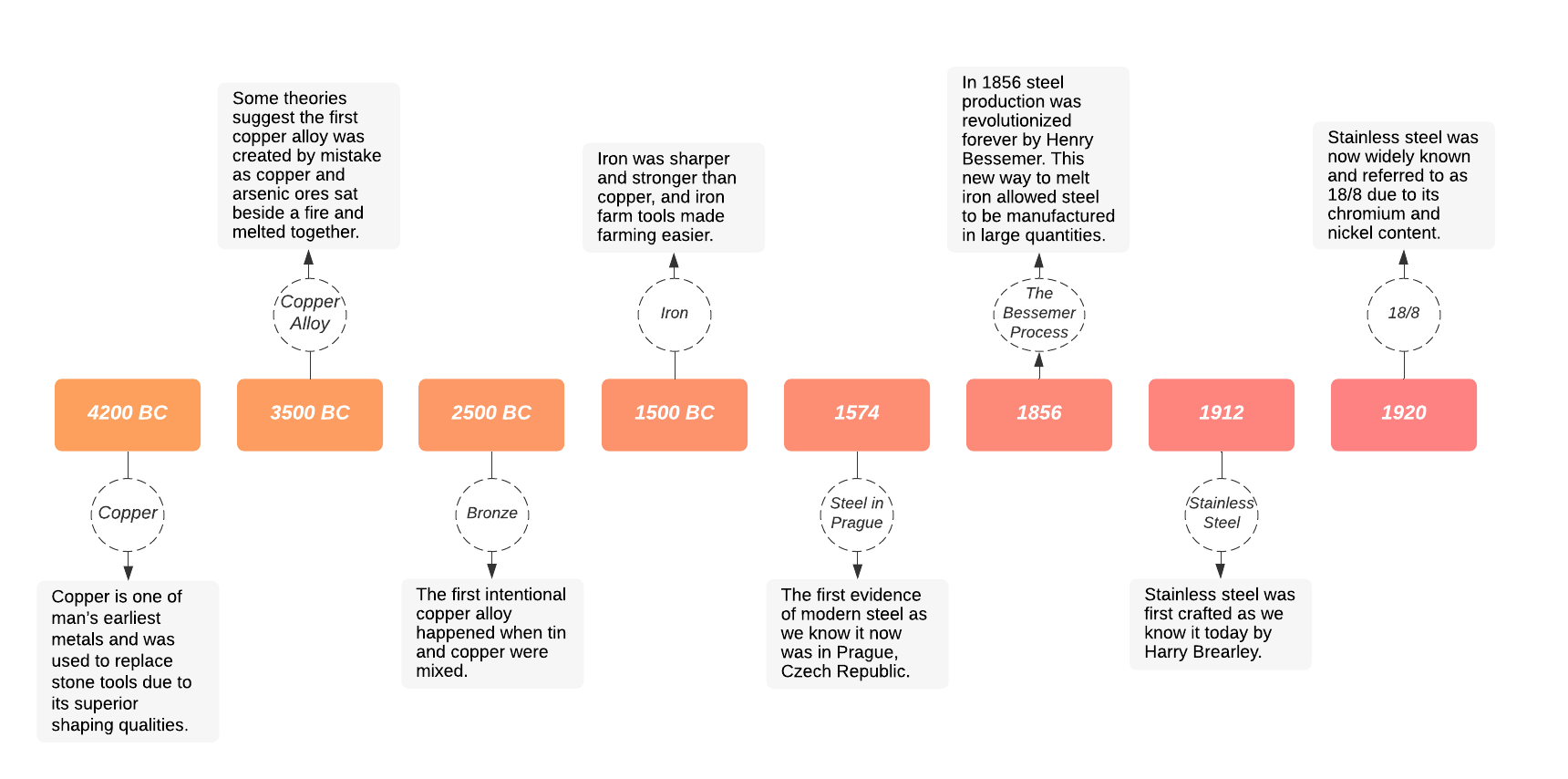
4200 – 2500 BC
Copper - Bronze
Copper is one of man’s earliest metals and was used to replace stone tools due to its supeior shaping qualities. Though copper’s exact origin is uncertain, archaeologists generally credit early Mesopotamians as the first to fully harness copper’s abilities. However, it is believed that this copper was mostly used for decorative purposes, since its relatively soft composition made it less than ideal for most tools.
The next step of progress was bronze, a copper alloy. An alloy is a metal that combines two or more metals or elements to create a new material.
Some theories suggest the first copper alloy was created by mistake somewhere around 3500 BC, as copper and arsenic ores sat beside a fire and melted together. Whether or not that is entirely true, the first intentional copper alloy happened later (2500 BC) when tin and copper were mixed, thus introducing bronze to the world. Bronze was stronger and superior to pure copper. This early combination would not be the last alloy to change the world.
1500 – 300 BC
Iron
Before there was steel, there was iron.
Iron was used for tools and weapons, and was superior to its predecessor, bronze. While bronze had required both copper and tin resources, iron was a single material that could be smelted at high heats. The abundance of iron made it extremely accessible, and those able to craft it immediately implemented it into all facets of life. Iron was sharper and stronger than copper, and iron farm tools made farming easier and tough ground more workable. Iron’s discovery also put weapons, such as swords and spears, into the hands of many for the first time, permanently changing the course of the world.
1574 – 1900
Steel
Steel is an iron alloy formed with a low amount of added carbon, which gives it additional strength. Though steel has been present within civilization for thousands of years, it was often difficult to work with and overall scarce. The first evidence of modern steel as we know it now was in Prague, Czech Republic in 1574, then in England by 1614. As the 17th century continued and the prevalence of steel rose, it became known that the best steel of the time was in Stockholm, Sweden.
In 1856 steel production was revolutionized forever by Henry Bessemer. The Bessemer process was a new way to melt iron. It used molten pig iron and airflow to melt and purify the steel. This process allowed steel to be manufactured in large quantities and for a relatively low price.
The new accessibility of steel, thanks to the Bessemer process, changed the way the world travelled and planned. Steel rails were considerably stronger and held up ten times longer than iron rails. Steel trains could withstand heavier loads, making railroad transportation more efficient. Additionally, steel’s strength made skyscrapers a possibility for the first time, permanently changing the way cities grew and operated.
1912 –
Stainless Steel
Stainless steel was first crafted as we know it today in 1912 by Harry Brearley. Brearley sought to form a corrosion resistant alloy for use in gun barrels. Amidst the process, one material remained rust free in the scrap heap. This martensitic stainless steel would later be known as the 420 grade.
By 1920 stainless steel was widely known and referred to as 18/8 due to its chromium and nickel content. With stainless steel’s growing popularity, its hygienic qualities were revealed. Stainless steel was corrosion resistant and safely used in 1928 to brew and hold beer, making it a prime material in the medical field and in food storage.
In 1931 stainless steel was used for aircraft for the first time. Though lighter materials such as aluminum and titanium are now preferred by the aerospace industry, stainless steel is still utilized for smaller pieces and parts. A few commonly used stainless steel grades in airplane parts are 13-8 MO, 15-5 PH, and 17-4 PH.
Stainless steel is now sorted into four general types with over 150 grades, and is used in millions of parts, machines, and other daily use items.